CENTER FOR RESEARCH AND TECHNOLOGY HELLAS (CERTH)
CHEMICAL PROCESS AND ENERGY RESOURCES INSTITUTE (CPERI)
LABORATORY OF ENVIRONMENTAL FUELS AND HYDROCARBONS (LEFH)
The Centre for Research and Technology-Hellas (CERTH) founded in 2000 is one of the leading research centers in Greece and listed among the TOP-20 EU research institutions with the highest participation in competitive research grants. CERTH consists of five institutes, including the Chemical Process and Energy Resources Institute (CPERI), whose mission is to conduct basic and applied research, to develop novel technologies and products and to pursue scientific and technological excellence in selected advanced areas of Chemical Engineering, including Energy, Environment, Materials and Process Technologies, in response to the needs of the Greek and European industrial and productive sector.
Within CPERI, the project is executed at the Laboratory of Environmental Fuels and Hydrocarbons (LEFH). LEFH is a catalytic reaction engineering laboratory of CPERI/CERTH that carries out fundamental and applied research in the area of refining and biorefining catalytic technologies. Emphasis is given on the development of catalytic processes for the production of fuels and chemicals with low carbon footprint according to the principles of circular economy (low-carbon conventional fuels, renewable and bio-based fuels, renewable chemicals from biomass and waste streams, etc.).
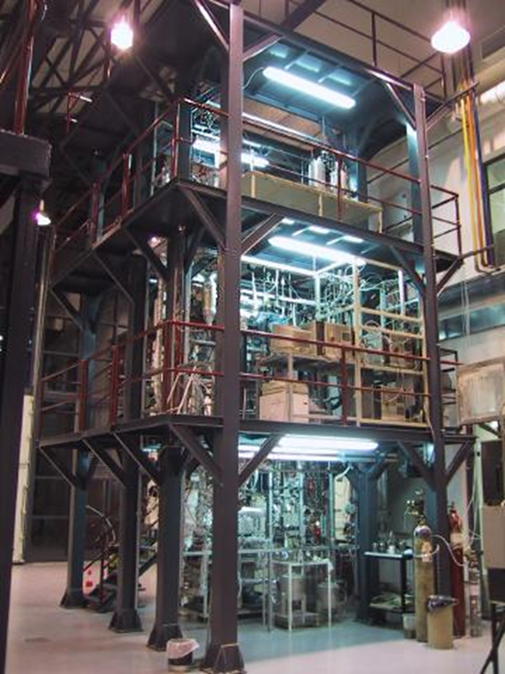
Fluid catalytic cracking (FCC) pilot plant for the aromatization of tyre pyrolytic oil
Research & Technological Activities
LEFH’s research focuses on (i) the development and optimization of industrial catalytic processes on small-, medium- and pilot-scale facilities; (ii) the synthesis of novel catalysts and the improvement of existing commercial catalysts; (iii) the advanced characterization of catalytic materials and the establishment of catalyst properties-performance relations; (iv) the investigation of catalyst deactivation and the development of regeneration processes and (v) the modeling and simulation of catalytic reactors and processes.
Moreover, LEFH offers advanced technical services to the petroleum-based and bio-based industries and catalyst manufacturing companies in (i) catalysts and catalytic additives evaluation and deactivation studies for the FCC process; (ii) process optimization studies for the production/upgrading of fuels and biofuels and (iii) characterization – quality specification of fuels and biofuels. LEFH has over 100 collaborations with refining and biorefining companies worldwide and participates in European projects, such as ABSALT (2021), NextGenRoadFuels (H2020), i3upgrade (RFCS), BIOCATPOLYMERS (H2020), BIOMATES (H2020), CASCATBEL (FP7), etc.
Role in BlackCycle
CPERI’s involvement in BLACKCYCLE is two-fold:
- optimization of the pyrolysis process of End-of-Life-Tyres (ELTs) by applying novel catalytic pyrolysis concepts and
- upgrading of the pyrolytic oil via catalytic processes, such as hydrodesulphurization (HDS) and aromatization.
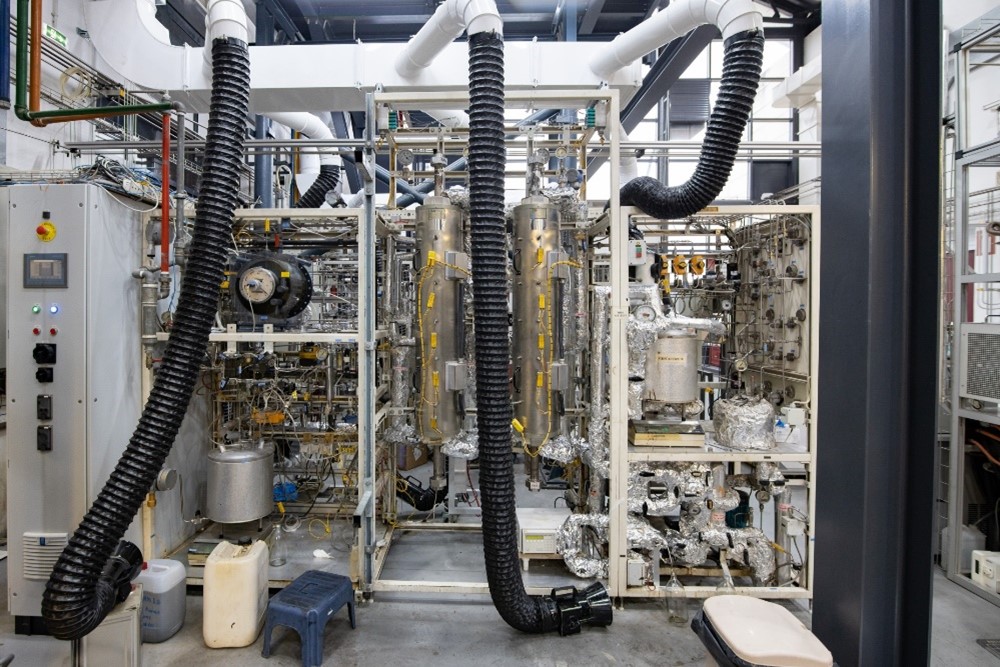
High pressure pilot plant unit for the hydrodesulphurization of tyre pyrolytic oil
With regards to pyrolysis, CPERI investigated the fast pyrolysis of ELTs, coupled with the cascade (ex-situ) catalytic upgrading of the pyrolysis vapors. Several metal and non-metal-promoted zeolites, as well as low-cost catalytic material prepared from natural sources, were synthesized and tested. The pre-screening showcased that the upgrading of the pyrolysis vapors was effective for the formation of aromatics, and that the type of catalyst could affect significantly the quality of the pyrolysis oil, producing oils with varying aromatic content and C/H ratios. The most promising catalysts from the pre-screening were tested in a continuous medium-scale experimental setup, where their performance was validated and the process conditions were optimized. The optimized process was subsequently demonstrated in a continuous pilot-scale catalytic pyrolysis unit with a bubbling bed thermal pyrolysis reactor and a circulating fluidized bed catalytic upgrading reactor with continuous catalyst regeneration.
The upgrading of the pyrolytic oil via HDS and aromatization processes aims to decrease the sulphur content and increase the aromatic content in the pyrolytic oil, respectively. The HDS process was optimized in a continuous high-pressure fixed-bed reactor unit by testing different commercial HDS catalysts based on sulphided Mo and by applying different reaction conditions. Aromatization on the other side, was investigated with different zeolites in a fixed-bed small-scale test unit, followed by upscaling the process in a circulating fluidized bed reactor a pilot unit
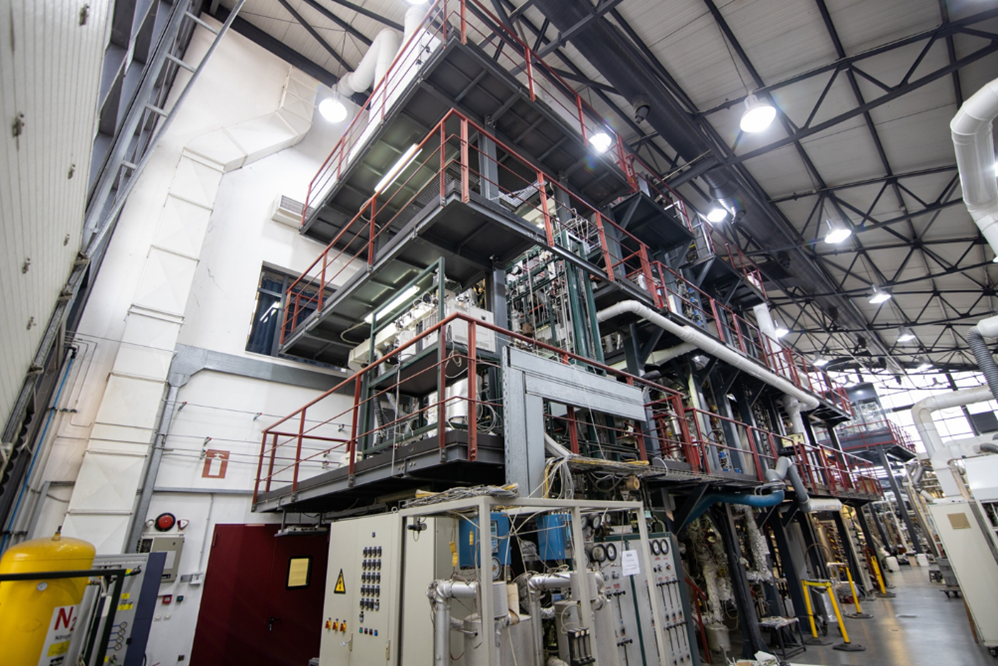
Pilot plant catalytic pyrolysis of ELTs